Tips for Building with Industrial IoT in Manufacturing
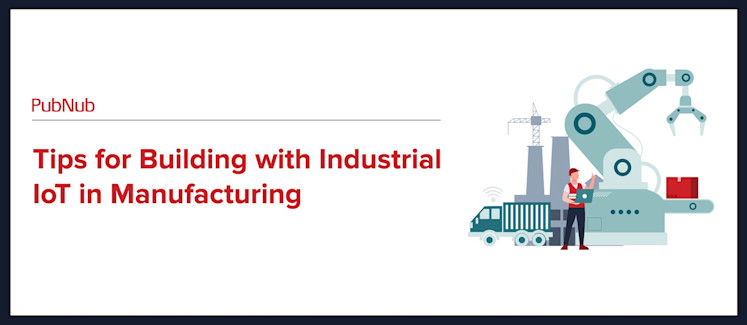
The Industrial Internet of Things (IIoT) plays a significant role in manufacturing processes across diverse sectors. It enables businesses to leverage real-time data and connectivity to drive digital transformation, optimize supply chains, and enhance production processes. As Industry 4.0 initiatives gather momentum, IIoT is increasingly seen as a critical enabler of intelligent manufacturing and automation, ultimately reducing downtime and improving overall operational efficiency.
The essence of implementing the Industrial Internet of Things in manufacturing lies in the core principles of digital transformation. This process involves adopting cutting-edge technologies such as artificial intelligence, machine learning, big data analytics, and cloud computing to revamp traditional manufacturing operations. Access to real-time data is crucial, as it empowers decision-makers to act quickly and make changes based on up-to-date information from various IoT devices and gateways.
Predictive maintenance is one of the most promising use cases of IIoT in manufacturing. This approach aims to prevent costly equipment failures by monitoring performance metrics and identifying signs of potential breakdowns before they occur. Using advanced data analytics algorithms and IIoT solutions, businesses can achieve comprehensive visibility into their production processes, enabling them to anticipate equipment failure, reduce bottlenecks, and perform timely repairs. This proactive approach reduces downtime and helps in optimizing the overall manufacturing operations.
In the following sections, we will dive deeper into predictive maintenance, explore the benefits of IIoT, and understand the impact of real-time data on manufacturing processes. We will also discuss overcoming some common challenges in implementing IIoT solutions, focusing on leveraging the capabilities of PubNub, a reliable real-time communication platform for IoT applications.
Leveraging Predictive Maintenance for Efficient Operations
Manufacturing industry stakeholders increasingly recognize the importance of implementing predictive maintenance strategies to minimize downtime and optimize equipment performance. By employing advanced IIoT technology and machine learning algorithms, businesses can accurately monitor and predict equipment failures, enabling them to address potential issues before they escalate.
To harness the power of predictive maintenance, the first step is to integrate IoT sensors and devices into the production machinery. These smart sensors collect real-time data related to equipment health, such as temperature, vibrations, and pressure. Ensuring seamless connectivity between IoT-enabled devices and data analytics platforms is critical for establishing a robust data-driven ecosystem.
Machine learning algorithms play a vital role in analyzing the vast quantities of data gathered by IIoT sensors to identify patterns and correlations between various metrics. This analysis helps anticipate potential equipment failures and alerts business stakeholders, facilitating proactive maintenance and reducing operational costs.
To implement an effective predictive maintenance strategy, businesses should focus on the following aspects:
Data Collection: Invest in a range of IIoT sensors, devices, and gateways to collect crucial data points from production machinery and processes.
Data Analysis: Utilize advanced analytics algorithms and machine learning techniques to process the collected data and derive insights to fuel decision-making.
Feedback Loops: Establish an ongoing feedback mechanism that enables technicians and engineers to act on the analyzed data, ensuring a continuous improvement process within the manufacturing operations.
Predictive maintenance, coupled with the intelligent use of real-time data and advanced analytics, can lead to substantial gains in equipment uptime, productivity, and overall operational efficiency. In the next section, we'll explore the benefits of harnessing the power of the Industrial Internet of Things (IIoT) and how it can enable businesses to thrive in the competitive landscape of modern manufacturing.
Harnessing the Power of Industrial Internet of Things (IIoT)
Adopting IIoT solutions significantly improves the manufacturing industry's operational efficiency and cost savings. Businesses can make real-time decisions and optimize workflows based on valuable insights using connected devices, sensors, and actuators to gather data from machines and processes.
Integrating IIoT with existing systems and equipment is essential for seamless connectivity and ensures the interoperability of various IoT devices and protocols within your network. By leveraging multiple data sources within their ecosystem, businesses can capitalize on the data collected and make insightful decisions that optimize production processes.
Robust security and privacy measures are crucial for successful IIoT deployments. Proper authentication and encryption protocols should be in place to safeguard data transmission and lessen potential cybersecurity risks. IIoT technology must comply with industry standards and regulations to ensure secure, reliable, and scalable solutions.
Consider these advantages provided by IIoT in manufacturing:
Improved Operational Efficiency: Access to real-time data enables informed decision-making, resulting in streamlined production processes and improved operational efficiency.
Cost Savings: Automated systems and predictive maintenance help minimize unexpected downtimes, reducing maintenance costs and mitigating potential asset management losses.
Enhanced Product Quality: Increased visibility into manufacturing operations and access to real-time data allows businesses to maintain tight quality control and promptly address product quality issues.
Flexible Production Line: The ability to quickly adapt to changes and implement data-driven strategies promotes agility and faster time-to-market.
Driving Digital Transformation in Manufacturing
Digital transformation plays a crucial role in modernizing manufacturing processes and staying competitive in the ever-evolving landscape of Industry 4.0. By implementing state-of-the-art tech advances, businesses can streamline operations, enhance product quality, and maximize efficiency.
Cloud-based platforms are an essential component of driving digital transformation, providing not only data storage but also enabling seamless collaboration, exchange, and analytics. Advanced analytics and machine learning tools are used to process large datasets gathered from multiple sources, deriving insights that facilitate data-driven decision-making and contribute to optimizing manufacturing processes.
Automation and robotics are cornerstones of digital transformation, offering benefits such as reduced operational costs, increased productivity, and enhanced worker safety. By automating mundane, repetitive tasks, businesses can free up human resources to tackle more complex and strategic projects.
To successfully drive digital transformation in manufacturing, organizations should focus on the following aspects:
Adopting Cloud-based Solutions: Utilize cloud computing platforms for data storage, collaboration, and analytics to streamline processes and reduce infrastructure costs.
Leveraging Advanced Analytics: Employ advanced analytics and machine learning techniques to make sense of vast amounts of data collected through IIoT devices and improve decision-making.
Implementing Automation and Robotics: Integrate automated systems and robotics into manufacturing operations, increasing productivity, efficiency, and safety.
Prioritizing Cybersecurity: Ensure robust security measures are in place to protect sensitive data and intellectual property from threats and attacks.
Next, we will delve into the impact of real-time data on manufacturing processes.
Real-Time Data and its Impact on Manufacturing
The significance of real-time data in manufacturing processes must be considered. It enables businesses to monitor operations closely, make informed decisions, and respond quickly to emerging issues or changes in production demands. Organizations can optimize their workflows by capturing and transmitting data in real-time, ensuring smooth operations and reducing disruptions.
Integrating IIoT sensors and devices into the production machinery enables businesses to collect and transmit vast quantities of data in real-time. This information at their fingertips facilitates quick decision-making, bolstering efficiency and innovation.
Real-time analytics further empowers organizations to make data-driven decisions that optimize processes and enhance overall operational performance. The benefits of leveraging real-time data in manufacturing include the following:
Improved Operational Visibility: Real-time data allows for comprehensive monitoring of the production processes, equipment health, and product quality, enabling faster identification and resolution of issues.
Quicker Decision-Making: Access to real-time information empowers decision-makers to quickly make informed, data-driven decisions, ultimately leading to better business processes and outcomes.
Proactive Hazard Management: Real-time monitoring of machines and equipment, along with predictive maintenance strategies, can help identify potential risks early, enabling organizations to take preemptive action.
Optimized Resource Allocation: Real-time data on asset performance, production rates, and equipment utilization allows businesses to allocate resources more effectively, improving overall efficiency.
Now let's look at how you can solve key IIoT challenges with PubNub.
Addressing Key Challenges with PubNub in Industrial IoT
As businesses adopt and implement IIoT solutions, they often face several challenges, such as scalability, data security, and low-latency requirements. PubNub is a reliable real-time communication platform for IoT applications, providing a robust solution to address these challenges and ensure seamless integration.
Scalability with PubNub's Global Data Stream Network
Scalability is a critical concern for businesses adopting IoT technology. As the volume of connected devices and generated data grows, ensuring reliable and consistent communication becomes increasingly challenging. PubNub's global data stream network is designed to handle extensive data traffic, delivering crucial real-time insights to enable businesses to make informed decisions regarding their manufacturing processes.
Data Security with PubNub's Built-In Security Features
Data security is paramount in the world of IIoT. Ensuring secure and encrypted data transmission is vital to protect sensitive information and maintain the integrity of your network. PubNub comes with built-in security features providing a trusted environment for data exchange.
Low-Latency Data Processing with PubNub's Edge Computing Capabilities
Latency is crucial in IoT applications, particularly regarding real-time data analysis and decision-making. PubNub's edge computing capabilities guarantee low-latency data processing, allowing businesses to react quickly to changes in production processes and equipment health, ultimately promoting overall efficiency and reducing downtime.
The final section will cover overcoming connectivity and integration challenges using PubNub and how its compatibility with various IoT frameworks can help businesses create a seamless and functional IIoT ecosystem.
Overcoming Connectivity and Integration Challenges with PubNub
One of the primary hurdles businesses face venturing into IIoT deployment is establishing seamless connectivity between various devices, protocols, and systems. PubNub offers a robust solution to address these challenges, ensuring secure and reliable communication for all components within the IIoT ecosystem.
Compatibility with Different Programming Languages and IoT Frameworks
PubNub is designed to work with multiple programming languages and IoT frameworks, making it adaptable to the needs of different manufacturing operations. This compatibility allows for simplified integration of PubNub into existing infrastructure and promotes interoperability among diverse IoT-enabled devices.
Integration with Existing Infrastructure and Legacy Systems
Modernizing traditional manufacturing processes often involves integrating new technology with existing infrastructure and legacy systems. PubNub's flexible APIs and SDKs allow for seamless integration, ensuring smooth communication and data flow across the entire manufacturing operation.
Pre-Built SDKs and APIs for Easier Device Integration and Data Exchange
To facilitate speedy implementation and reduce development time, PubNub provides pre-built SDKs and APIs, simplifying the process of connecting IoT devices to the platform. With these tools, businesses can easily enable secure data exchange amongst various components of their IIoT ecosystem, driving efficiency and boosting productivity.
PubNub's real-time communication platform is pivotal in building a robust, secure, and scalable IIoT environment. By addressing the challenges of connectivity, integration, data security, and latency, PubNub allows for the seamless implementation of IIoT solutions, empowering businesses to harness the power of real-time data and transform their manufacturing processes.
To get started with PubNub and use these powerful real-time API features, sign up for a free trial or contact our sales team.