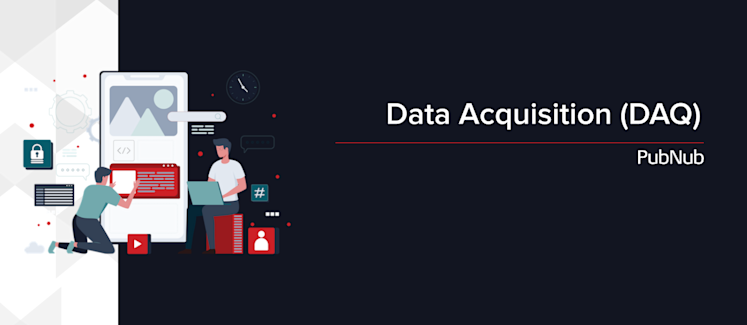
Data Acquisition Definition
Data acquisition (DAQ) is the process of collecting real-world analog signals from sensors or transducers, converting them into digital data using Analog-to-Digital Converters (ADC), and transmitting them to a computer or processing system for analysis, monitoring, or control. Key components include sensors, signal conditioning, ADC, multiplexers, and timing/synchronization mechanisms. DAQ is crucial for industrial automation, scientific research, and IoT, enabling real-time or batch data capture for decision-making and system optimization.
1. Components of Data Acquisition Systems
A typical Data Acquisition System (DAQ) consists of several essential components:
Sensors/Transducers These devices convert physical phenomena such as temperature, pressure, humidity, or light into electrical signals. For instance, a thermocouple can measure temperature by generating a voltage proportional to the temperature difference between two junctions.
Signal Conditioning Before the sensor signal is digitized, it often needs to be amplified, filtered, or otherwise conditioned. This stage ensures the signal is at the appropriate voltage level and clear from noise. Some examples of signal conditioning include:
Amplification: Scaling the signal for proper interpretation by the ADC (Analog-to-Digital Converter).
Filtering: Removing unwanted noise (e.g., high-frequency interference) using low-pass or band-pass filters.
Analog-to-Digital Converter (ADC) An ADC converts the conditioned analog signal into a digital format. ADC resolution is critical here. For example, an 8-bit ADC can represent 256 discrete levels, while a 16-bit ADC can represent 65,536 levels, making it more suitable for capturing fine details in the signal.
Multiplexer (MUX) When multiple sensor signals need to be acquired, a multiplexer is often used to sample them in sequence. The MUX reduces hardware complexity by allowing multiple inputs to share a single ADC.
Timing and Synchronization Precise timing and synchronization are essential, especially when capturing high-frequency signals or when correlating data from multiple channels. This is often achieved using timers and clock circuits.
Data Storage and Transmission After conversion, data must be either stored locally or transmitted to a remote system for processing. Storage media range from high-speed RAM for temporary data retention to long-term storage devices like SSDs or cloud servers. Data transmission protocols can vary depending on the application, with USB, Ethernet, and wireless communication like Wi-Fi and Zigbee being common.
2. Types of Data Acquisition Systems
There are different types of DAQ systems designed to meet various needs. These include:
PC-Based DAQ Systems a computer equipped with data acquisition hardware (e.g., DAQ cards) handles data processing and storage. For example, National Instruments (NI) offers DAQ modules that interface with LabVIEW software for control, visualization, and analysis.
Standalone DAQ Systems operate independently of a computer, with onboard processors for signal acquisition and storage. Such systems are used in remote or hazardous environments where a PC cannot be placed. Standalone DAQs are often found in industrial automation, like the Yokogawa GX series, which can handle multiple channels in real-time.
Distributed DAQ Systems allow data to be captured at different locations and combined centrally. These systems are highly scalable and used in smart grids or large-scale environmental monitoring. They can leverage IoT technologies for wireless communication between acquisition nodes and a central server. Distributed DAQ systems are essential in big data environments where sensors collect vast amounts of information from multiple sources.
Modular DAQ Systems are designed for flexibility and scalability. Users can add or remove modules based on the specific sensors or measurement types they need. PXI (PCI eXtensions for Instrumentation) is a widely used modular platform, often paired with specialized software like MATLAB for advanced analytics.
3. Data Acquisition Process
The data acquisition process can be broken down into the following steps:
3.1. Sampling
Sampling is the process of converting a continuous-time signal into a discrete-time signal by taking measurements at regular intervals. The sampling rate (frequency) must be at least twice the highest frequency component of the signal, as per the Nyquist-Shannon sampling theorem, to avoid aliasing. For instance, if you're sampling a signal with a maximum frequency of 10 kHz, your sampling rate should be at least 20 kHz.
3.2. Quantization
Quantization is the step where the continuous amplitude of the sampled signal is approximated by discrete levels. The number of quantization levels depends on the resolution of the ADC. A higher-resolution ADC leads to finer quantization, which improves accuracy but may increase system complexity and data size.
3.3. Data Acquisition Modes
Data can be acquired in different modes based on the application's requirements:
Single-ended mode: All signals share a common ground, which can introduce noise, especially for low-amplitude signals.
Differential mode: Each signal is measured relative to its own reference, which reduces common-mode noise and improves signal integrity.
3.4. Data Transfer
The acquired data can either be:
Buffered: Data is stored in memory temporarily before being transferred for analysis.
Streaming: Data is sent continuously to a storage system or processing unit, essential for real-time monitoring applications like vibration analysis in rotating machinery.
4. Challenges in Data Acquisition
Despite its importance, data acquisition presents several challenges, especially in large or high-speed systems. These include:
Noise and Interference Electrical noise from other systems can distort sensor readings. Shielded cables, proper grounding, and signal conditioning techniques are employed to mitigate these issues.
Data Integrity High sampling rates or large-scale distributed systems generate massive volumes of data, making it essential to ensure data integrity during transmission or storage. Error-checking protocols like cyclic redundancy check (CRC) are often implemented.
Latency In real-time systems, delay between data capture and processing can be a concern, especially in critical applications like medical devices or industrial control. Low-latency communication protocols like EtherCAT are designed for these applications.
Scalability As the number of sensors increases in applications like telemetry or IoT or environmental monitoring, the DAQ system must scale to handle more data without compromising performance.
5. Real-world applications of Data Acquisition
Industrial Automation DAQ systems monitor and control manufacturing processes, collecting data from temperature sensors, pressure gauges, and flow meters to ensure optimal performance. For instance, in a petrochemical plant, DAQ systems continuously monitor the conditions in reactors to prevent dangerous conditions like overheating.
Healthcare Medical devices like ECG (electrocardiogram) machines rely on telemetry DAQ systems to capture electrical signals from the heart. These signals are then analyzed to detect abnormalities in heart rhythms.
Environmental Monitoring DAQ systems collect data from sensors deployed in the environment, measuring parameters like air quality, water levels, and radiation. Distributed DAQ systems are used to gather data from remote locations and aggregate it for central processing.
Automotive Testing In the automotive industry, DAQ systems are used to capture data during vehicle testing, measuring parameters like engine temperature, vibration, and acceleration. This data is critical for assessing vehicle performance and safety.
Conclusion
Data acquisition plays a foundational role in modern technology, enabling systems to interact with the physical world by transforming raw sensor data into actionable insights. Whether in industrial control, healthcare, or research, DAQ systems provide the backbone for data-driven decision-making. However, understanding the nuances of sampling rates, signal conditioning, noise reduction, and scalability is crucial for designing efficient and reliable systems.
How PubNub can help with data acquisition?
PubNub can significantly enhance data acquisition by enabling real-time, low-latency communication between sensors, devices, and centralized data processing systems. PubNub’s platform provides a robust framework for data streaming, allowing sensors or IoT devices to continuously send real-time data to cloud services or analytics systems, facilitating instant processing, analysis, and decision-making.
With PubNub's Illuminate product, developers gain deeper insights into their data streams. Illuminate provides real-time observability and monitoring capabilities, allowing users to visualize, trace, and analyze data as it flows through PubNub’s infrastructure. This ensures that any issues, such as data anomalies, latency spikes, or connection failures, can be quickly identified and addressed, improving the reliability and efficiency of data acquisition processes.
Key ways PubNub aids data acquisition:
Real-Time Streaming Ensures continuous data flow from sensors or devices to processing systems, critical in applications like industrial monitoring or IoT ecosystems.
Scalability Handles high volumes of data from distributed sensors without compromising performance, making it ideal for big data applications.
Global Presence With low-latency data transmission across PubNub’s global network, data acquisition systems can operate across regions with minimal delay.
Event-Driven Architecture PubNub supports triggering real-time actions based on data, such as anomaly detection or real-time alerts.